If we take a look at the shipping industry, we would see that one of the most common challenges faced by them is that of real-time freight analytics. With the increasing competition and customer demands, new and improved analysis and response methods are highly required. This brings to the fore the requirement of digital supply chain visibility tools. Since analytics provide supply chain ecosystem clarity, such tools can help retain competitive advantage through collaborative logistics.
Having said that, a common dilemma amongst those organizations who work with global logistics operations is if the benefits of products focused on the digitization of the supply chain are worth the money. While there is no easy answer to the question, you can take a look at all the aspects under the Return on Investment (ROI) umbrella to at least simplify the thought process.
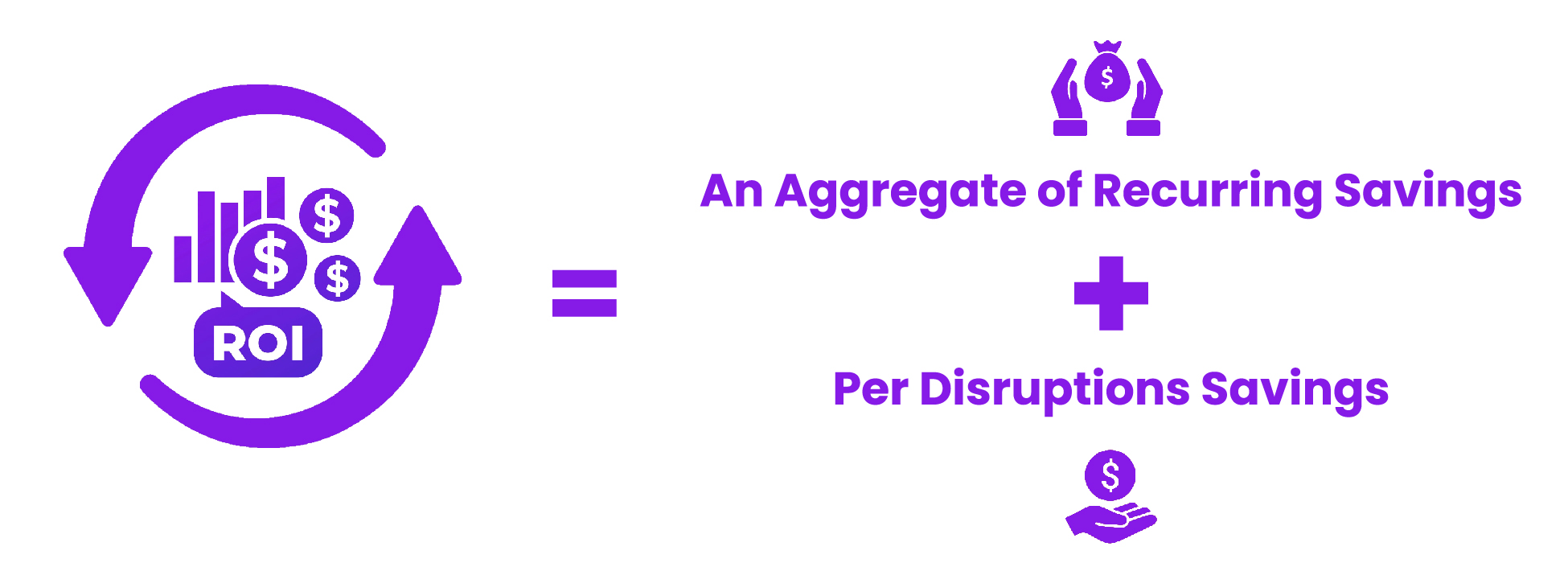
Keeping this in mind, Recurring Savings = Manual Resources Savings + Insurance Savings + Procurement Savings and Per Disruption Savings = Crisis Containment + Inventory Cost.
How can Supply Chain Visibility Tools Benefit Your Business ROI
As you look into specific subjects, you can start identifying common themes across industries. With this in mind, some of the benefits of incorporating supply chain tools to measure and maximize ROI for real-time transportation visibility include:
Improvement in the Efficiency of Resources & Faster Resolution to Conflicts
As part of the logistics and transport industry, your main aim would be to deliver on the company’s strategy efficiently. One of the most important aspects of this includes the real-time track and trace and how this impacts the execution of operational tasks. By incorporating a supply chain automation tool that offers real-time data, you can reduce phone calls for customers’ information requests by a large freight forwarder by 1.5 times.
With this, even when you have several contractual supply chain partners, you can look at all of them at once, thereby increasing productivity and gains to the overall strategy for better ROI. This would give you almost $300,000 of projected annual savings for a mid-sized distributor.
As you streamline managing and keeping track of several contractors, ensuring that the invoices are in proper order shouldn’t be complicated with a supply chain automation tool. You can have updated information from all the vendors which would help anticipate the costs of demurrage and detention, thereby allowing you to automatically eliminate any extra step and maintain a verification system that reduces almost two days taken to invoice.
Reducing any Costs Related to Errors and Documentation
Talking about the vital processes in international commerce, customs clearance comes on top of the list. Collecting the information from various sources, documents and then transitioning the selected parts to the customs clearance declaration takes a lot of effort. However, human errors are inevitable, and even the tiniest of them can jeopardize the company’s brand value in front of the Customs Authorities. You might even have to start the process from the beginning altogether. The cost of demurrage and detention, along with generating a new document is high, and so is the time taken.
By incorporating a supply chain automation tool, you digitize the trade documentation and thus reduce any potential errors in customs clearance and standardization. This would ensure that the data from the Bill of Lading will automatically fill up the customs declaration and other feeding partners with digital copies of the documents. It would ultimately lead to saving a lot on the time and money spent in the entire process. As the Customs Authorities are becoming digitized slowly but steadily, by investing in new tools, you can minimize the mistakes caused by manual entries, thereby freeing up somewhere around 100 hours of administrative work.
Tracing and Tracking to Reduce the Risk of Cargo Losses
A common but global problem most companies face is that of cargo theft. While there are countries that face it to a lesser extent, a large number of them, especially when they’re shipping expensive items, are targeted a lot. The long transit time between the port and the warehouse makes it almost impossible to figure out where the burglary happened. This has made several companies budget a default ‘losses to theft’ amount right from the get-go.
However, with supply chain automation tools that offer real-time data and statistics, you can monitor every stage of the transport, thereby enabling you to pinpoint the exact point of burglary (if and when it happens). The detailed milestones for tracing and tracking containers received from the operators help you find the deviations easily. This ensures that you save almost eighteen days in the BL process from the issuance to surrender by the reefer exporter, ultimately increasing the shelf-life of perishable cargo and reducing the risk of spoilage.
The unreported delays and the unresolved issues can automatically create a ripple effect on the productivity of a supply chain, and keeping that in mind, Timber Exchange has come up with a custom supply chain management automation software. Specializing in the timber industry, aptly named Timber Exchange, the platform helps you digitize the whole process – starting from inquiry to delivery.
With no requirement for physical documentation, meant for importers, exporters, and freight forwarders, you can raise demands for timber, supply the products, and keep track of the entire cargo from the comfort of your home or office. To know more about this plug-and-play model or talk to the experts, feel free to book a demo session.