At Centersource Technologies AB we are committed to the highest standards of ethical research and data integrity, guided by the ESOMAR Code of Conduct. Our data is sourced from a limited, anonymous market survey conducted with trusted and established industry participants. The insights derived from this survey reflect aggregated finalized prices as well as observed prices reported within the participants respective markets, with a focus on the highest prices recorded during the first two weeks of each month. These insights are provided for informational purposes only and are intended to indicate market trends rather than serve as comprehensive or fully representative market data.
In adherence to ESOMAR's principles, we ensure that all data collection and analysis are conducted with transparency, respect for confidentiality, and strict compliance with ethical guidelines:
- Data Sourcing and Methodology:
We exclusively use data from government, customs, or government-affiliated websites to maintain reliability and public integrity. In addition, we engage directly with industry experts to gather real-time, firsthand information. Each data point is collected, verified, and aggregated following established ethical standards, ensuring that our research processes meet the rigor recommended by ESOMAR. - Transparency and Accuracy:
All data are published promptly as they become available from the source, ensuring that our insights remain current and reflective of on-ground market dynamics. We actively seek and incorporate regular feedback from industry experts, which allows us to make real-time adjustments and continuously improve the accuracy and reliability of our data. - Ethical Data Usage and Third-Party Material:
Our adherence to the ESOMAR Code of Conduct underscores our commitment to ethical research practices. We maintain strict controls over data sharing and usage; copying or distributing our data is prohibited under our company policy. Furthermore, all necessary agreements are in place for any third-party material used, ensuring full compliance with copyright laws and industry best practices. - Limitation of Liability:
While we strive to provide high-quality, timely market insights, the data is derived from a limited sample and should be interpreted within that context. We are not liable for any damages arising from the use of this data, as it is provided solely for informational purposes and as a directional indicator of market trends.
By integrating ESOMAR's ethical guidelines into our research methodology, we ensure that our practices are transparent, respectful of data confidentiality, and aligned with internationally recognized standards. This commitment not only reinforces the credibility of our insights but also builds trust with our stakeholders and industry partners.
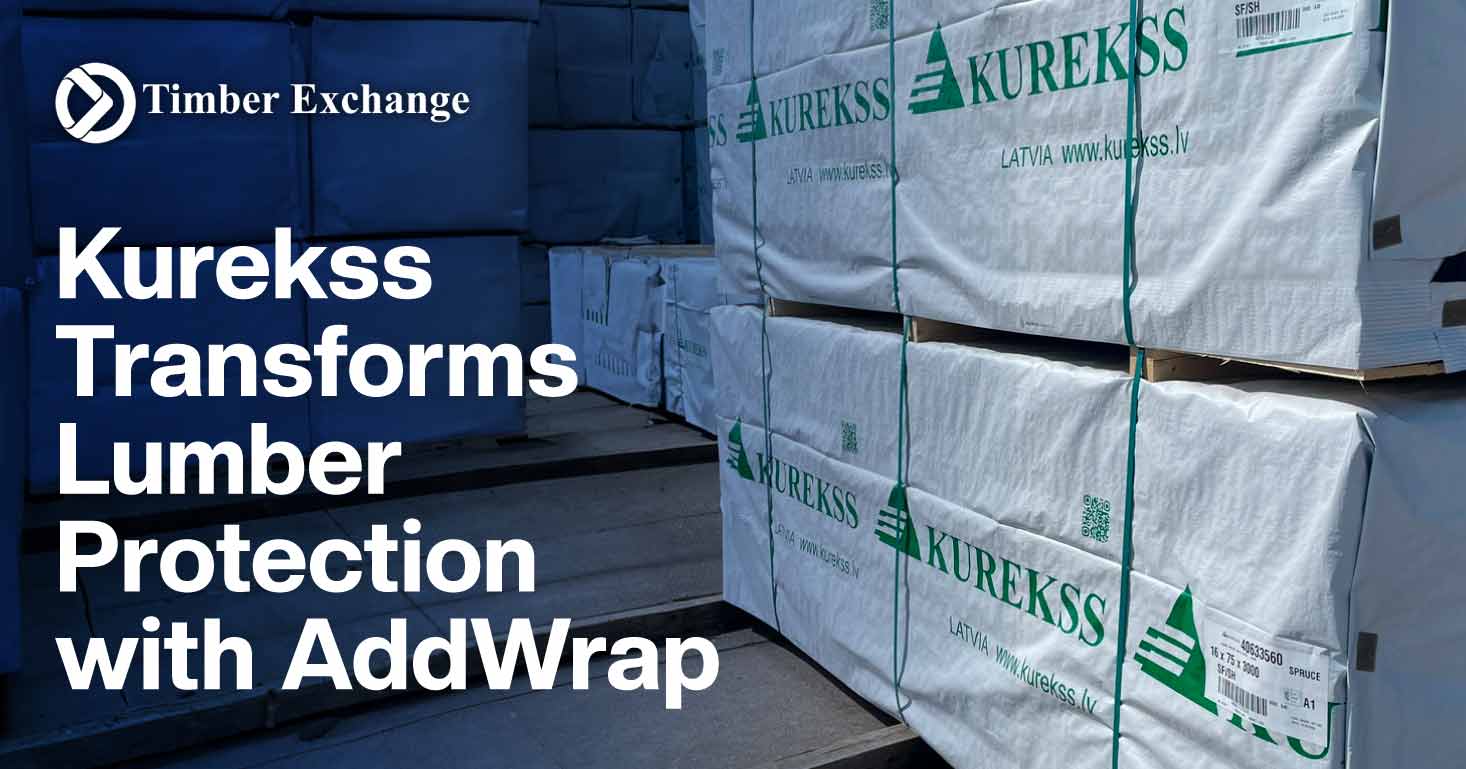
Kurekss Transforms Lumber Protection with AddWrap
Posted on September 25, 2024 |
As environmental concerns and operational efficiency become increasingly important in the global timber industry, companies are exploring strategies for minimising waste without compromising product quality. Kurekss, one of Latvia's leading sawmills, recently made a significant shift in how they protect their lumber, opting for woven wraps from AddWrap in place of traditional blown film wraps.
Dzintars Rasa, the production manager at Kurekss, discussed the challenges his team faced and the rationale behind their move toward a more sustainable solution.
Addressing Challenges in Lumber Protection
Kurekss had long relied on conventional plastic wraps to protect their lumber. However, as Dzintars explains, these wraps were no longer meeting their needs.
According to Rasa, the films used were blown films. They would tear very easily, meaning this lot had taken up quite a bit of plastic. Further, they lacked breathability, thus risking moisture build-up, a nemesis for the integrity of the lumber.
For a company handling large volumes of lumber, such inefficiencies were difficult to ignore. Kurekss began searching for an alternative that could provide better protection while also aligning with their environmental goals.
A Shift Toward Sustainability
The decision to switch to AddWrap’s woven wraps was driven, in large part, by a desire to reduce plastic consumption. As global industries face increasing pressure to adopt greener practices, Kurekss saw an opportunity to improve both its operational processes and its environmental footprint.
“We’re covering the same volume of wood but using far less plastic than before. It’s a massive win for us," Dzintars explains. "There’s a good reduction in plastic consumption, and with global pressure to reduce environmental impact, we needed a solution that wasn’t just strong but eco-friendly too.”
The new woven wraps use just 72 grams of plastic per square meter, a fraction of what traditional plastic films require. This shift not only contributes to Kurekss' sustainability efforts but also enhances the durability and breathability of their lumber protection.
Practical Benefits: Strength and Breathability
In addition to reducing plastic use, Kurekss found that the woven wraps outperformed their previous materials in terms of strength and function. The wraps, while lightweight, provide enhanced resistance to tearing and damage.
The woven wraps were very strong, and they did not experience any of the problems that they experienced with the blown film. The breathability of the wraps was also such that nobody would be worrying about moisture getting trapped and damaging the wood.
This combination of durability and breathability is particularly important in sawmills, where maintaining the integrity of the lumber is crucial for both quality and cost management. In this way, AddWrap's product prevents moisture from accumulating, resulting in costly losses.
A Broader Industry Trend?
Kurekss’ transition to woven wraps may signal a broader trend in the global timber industry, where companies are increasingly looking for solutions that strike a balance between performance and sustainability. For Dzintars and his team, the decision to move away from traditional wraps has been a positive one, offering both practical benefits and environmental improvements.
"Their woven wraps have made it easier to protect our lumber while using less plastic, which has been a huge plus for both our business and the environment," Dzintars says. "the strength and breathability of their products really stand out."
Looking Ahead
As companies make more and more efforts to cut waste and efficiency improvements are embedded among their challenges, the Kurekss experience can be a model for other companies planning to make similar changes. The sawmill is happy with the results at the moment. Dzintars thinks more businesses will eventually follow suit.
Although using woven wraps is still a relatively new practice in some industries, success on the part of Kurekss demonstrates that innovative solutions can deliver sustainability along with operational improvements while maintaining performance.